O compressor de parafuso foi inventado por Alf Lysholm, professor do Royal Swedish Institute of Technology, em 1934. Sua intenção original era sobrecarregar motores a diesel e turbinas a gás. De acordo com estatísticas relevantes: durante 3.000 horas de operação, a falha da unidade de pistão é 10 vezes maior que a da unidade de parafuso; durante 12.000 horas de operação, a falha da unidade de pistão é 4 vezes maior que a da unidade de parafuso. A máquina de parafuso é do tipo rotativo e sua amplitude é 1/5 da máquina de pistão, portanto a vibração e o ruído são relativamente pequenos. Atualmente, os compressores de parafuso com injeção de óleo tornaram-se os principais modelos nas áreas de aerodinâmica e refrigeração e ar condicionado. No dispositivo aerodinâmico de fluxo de volume médio e no dispositivo de refrigeração com capacidade média de resfriamento, ocupa a participação dominante no mercado. Nas indústrias alimentícia, médica e outras, os compressores de parafuso isentos de óleo são altamente considerados como compressores de processo novos, limpos e eficientes.
A parte central do compressor de parafuso é o rotor de parafuso. A natureza avançada do perfil do rotor determina o desempenho de toda a máquina, e os requisitos de precisão de processamento e tratamento térmico de superfície são muito altos. Se a linha de moldagem mais avançada pode ser processada tornou-se um símbolo de medição da força econômica e técnica de uma empresa de usinagem. Atualmente, o perfil do rotor foi desenvolvido para a terceira geração - perfil assimétrico, incluindo principalmente o perfil alemão GHH, o perfil Hitachi do Japão e o perfil Atlas Copco SAP da Suécia, usando 5 a 6 perfis de dentes assimétricos. Equipamentos de processamento de parafusos e equipamentos de medição e teste são basicamente importados do exterior, incluindo principalmente o centro de usinagem britânico HOLROYD, MAUSER alemão, DEA italiano, sistema de medição de três coordenadas IMS britânico, mas os preços são muito caros, muitas vezes dezenas de milhões de yuans, e as empresas comuns não podem pagar pela compra e manutenção de rotina, então alguns fabricantes de unidades de refrigeração nacionais têm duas opções ao produzir ou fornecer: uma é "trazer", ou seja, compressores ou peças de cabeçotes de máquinas são adquiridos diretamente de fabricantes profissionais estrangeiros. Atualmente, as marcas internacionais de compressores de qualidade relativamente alta incluem HANBELL de Taiwan, Fusheng, BITZER da Alemanha, Grasso, REFCOMP da Itália, Fujihao, COMA, Hitachi do Japão, Daikin, Mitsubishi Heavy Industries, Kobelco, FRICK dos Estados Unidos, Atlas Copco da Suécia ; Evaporadores, condensadores, desengordurantes, etc. são processados internamente, além de alguns componentes de controles elétricos importados (como controladores programáveis industriais PLC, telas sensíveis ao toque de terminais programáveis, filtros, válvulas de expansão térmica, etc.) são montados e enviados. . A segunda é a "autossuficiência", ou seja, exceto os componentes de controle elétrico, os componentes do cabeçote da máquina, evaporadores e condensadores são todos processados e produzidos por si próprios. A escala da empresa é geralmente relativamente grande e todos os equipamentos de fundição, processamento e teste são importados.
Para garantir o funcionamento normal, seguro e confiável do compressor, é necessário garantir que outros componentes da unidade, incluindo o condensador, evaporador, válvula de estrangulamento ou expansão, funcionem normalmente, e uma série de componentes de controle também são necessários para controlar os parâmetros de temperatura e pressão durante a operação do compressor. Detecção e feedback em tempo real, e a operação normal de toda a máquina são coordenadas pelo controlador programável industrial. Essas funções de proteção automática devem incluir proteção de alta e baixa tensão, proteção de nível de óleo, proteção contra superaquecimento de exaustão, superaquecimento do motor e proteção contra sobrecorrente, perda de fase e proteção de fase reversa. , proteção contra corte de água, proteção anticongelante, etc., para parar automaticamente o sistema, bloquear a falha, exibir informações de alarme/aviso e emitir um sinal de alarme em caso de anormalidade no sistema.
As unidades de refrigeração são geralmente equipamentos de alto consumo de energia e seus requisitos de economia de energia durante a operação são muito importantes. É necessário que a unidade possa ajustar automaticamente o estado operacional de acordo com as alterações de carga externa para garantir que a unidade opere sob a carga ideal. Ao mesmo tempo, a unidade deve ter desempenho de carga parcial, ou seja, pode operar efetivamente com carga menor e quando a temperatura da água da torre de resfriamento estiver baixa, e realizar regulação contínua. Naturalmente, quanto mais amplo for o intervalo de regulação energética, melhor. No projeto de sistemas de refrigeração, economizadores econômicos são frequentemente usados para fazer parte do líquido refrigerante passar pelo resfriamento intermediário para melhorar o grau de subresfriamento, melhorando assim a capacidade de refrigeração por unidade de meio de trabalho. Em termos de medição da economia de energia da unidade, a capacidade de refrigeração por unidade de potência de entrada é um parâmetro importante, e os equipamentos sofisticados podem atingir mais de 4,5W/W, também conhecido como índice de eficiência energética ou coeficiente de desempenho, que é expresso pelo COP (Coeficiente de desempenho).
Uma interface homem-máquina amigável também é uma parte essencial de uma unidade de refrigeração bem feita. Geralmente é necessário usar uma operação de tela de toque de controlador programável de nível industrial com uma interface totalmente chinesa. Este modo combinado é simples e fácil de entender, com forte capacidade anti-interferência e alto grau de automação. Os operadores podem alterar livremente as configurações dos parâmetros de acordo com as necessidades reais de produção e ter múltiplas funções, como "exibição do status de execução", "exibição da causa da falha", "exibição do tempo de execução cumulativo", etc. para consultas históricas e manutenção
.
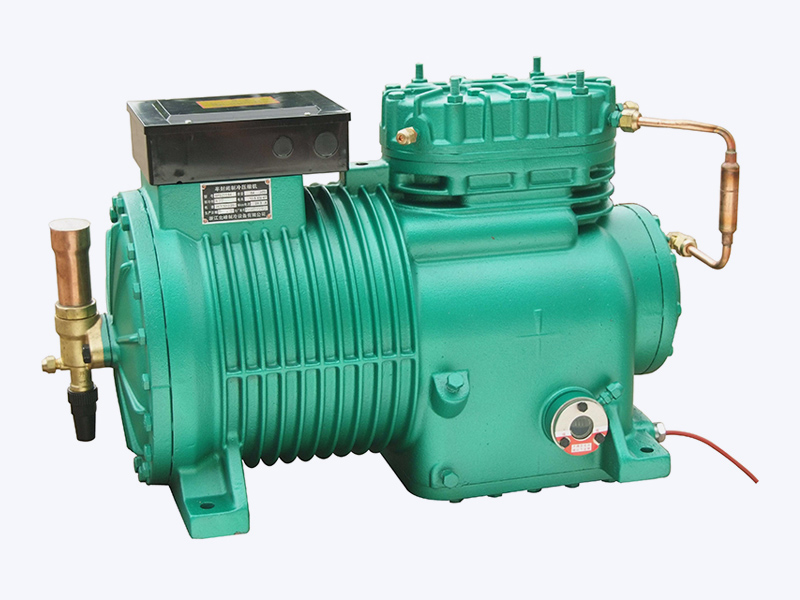